3D Printer produces first bio-polymer concept product for the marine sector
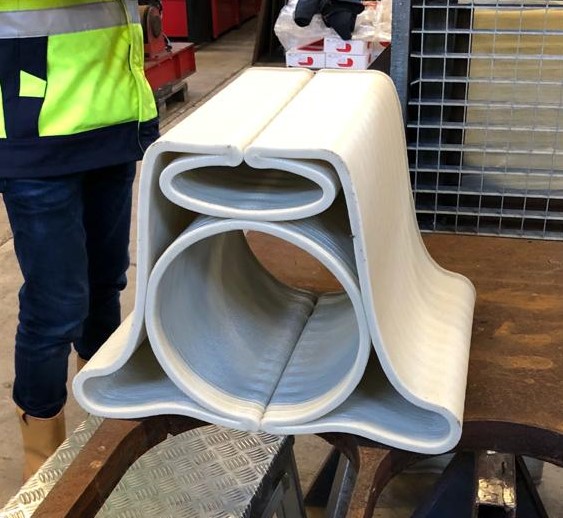
SeaBioComp has produced its first 3D printed biopolymer fender profile for use in the marine environment.
The fender profile was printed on an FDM Printer by Poly Products, a Netherlands based composite production and specialist engineering business, and partner in the SeaBioComp project, in collaboration with de Klerk Waterbouw who specialise in the installation of products for the marine environment.
SeaBioComp funded the research into the adaptations required to enable the 3D printing machine to process biopolymers which was undertaken by Poly Products. Research and testing into temperature control, natural fibre selection and corrosion of extruder parts were all thoroughly reviewed.
Project observer partner, De Klerk Waterbouw wanted to investigate the design and production of a bio-composite vertical fender profile for the berthing and guiding of ships, in order to replace traditionally used tropical hard woods and synthetic plastics. Collaboration with industry, end users, research establishments and public authorities is a key part of the SeaBioComp project, so a number of partners worked on the design, material selection, 3D printing, testing and evaluation of a scaled version of the biopolymer fender profile.
The findings from the material testing led by the University of Portsmouth and mechanical testing by De Klerk Waterbouw show very promising results and further optimization of designs, materials and production may lead to future full-scale production.
Commenting on the success of the 3D printing, Dr Albert ten Busschen, Poly Products, said: 'Using our 3D-printing technique, products can be made directly without the need of a mould. This saves the use of material and time. Moreover, there is no material spillage when a product is produced because no trimming or machining is necessary. Within the SeaBioComp project it is important that biopolymers can be printed with our 3D-printer. We printed the biobased polymers Thermoplastic Starch (TPS) and Poly Lactic Acid (PLA) on our machine to prove that we can make sustainable products for marine applications. Together with De Klerk we are now pursuing the development of full-scale fender profiles printed with biopolymers. We have completed mechanical tests and are now planning to print and install a full-scale printed fender profile with De Klerk to see how it works in practise.'
Ivo van Dalen, technical project leader of De Klerk Waterbouw is very enthusiastic: 'De Klerk Waterbouw has installed hydraulic engineering structures for over 150 years. We make large structures in docks and harbours from traditional materials like steel and tropical hardwood. But we are always open to new innovations and feel the responsibility to support a sustainable society. The SeaBioComp project opens possibilities for our company to make developments in that direction. The cooperation with Poly Products is very productive: we have jointly developed new, efficient and biobased fender profiles for berthing structures. With the production of full-scale prototype profiles we will undertake practical tests on the quay at our premises. Both our companies are oriented to develop solutions that are practical and efficient.'
The reports into the adaptations required for 3D printing of biocomposites and details of the 3D printed fender are available as downloads from the website. http://www.seabiocomp.eu/downloads/
Send this story to a colleague